Mastering Inventory Management: How Advanced Order Export for WooCommerce Can Help Your Business Thrive
Table of Contents
Cash is king in any business, including manufacturing. As we all know, inventory management is vital in lean manufacturing. Therefore, minimizing “working capital”— cash tied up in physical assets— should be a priority for any manufacturer looking to optimize efficiency and cash flow.
It goes without saying that any company must ensure that these inventories do not run out, with the risk of missing an order deadline, unhappy customers and associated reputational damage.
On the other hand, ensuring there is sufficient inventory should not mean that there will be so much of it on site that cash flow will be negatively impacted, or that products will die or become obsolete before they are used. This is especially true for companies seeking to adhere to lean manufacturing principles.
Why Does Inventory Management Matter?
Good inventory management planning is essential for the growth and development of any company. Without a good management system, there may be shortages of products or items that are in stock for a long time. Both cases entail financial losses for the company. Through effective inventory management, a company will always have the materials it needs to produce goods and serve customers. It will also be able to maintain the quality of its products and delivery times.
An inventory management system simplifies and automates company processes. Find out more about the main advantages of this technology:
- Sector integration
Process automation allows you to integrate all sectors of the company. This is because the solution records the products supplied by the supplier and indicates that they are already in stock. When there is a problem with a product, this is also recorded by the system, which generates a notification. It helps track sales and also provides data for the financial sector. At the same time, all processes are centralized, which reduces the number of errors when calculating taxes.
- Purchase Forecast
Another benefit of having an inventory and storage management system is the ability to forecast purchase needs. The manager can set minimum and maximum inventory limits so that the system can track and notify when you need to be restocked an item. This helps in decision making and tracking the number of sales of each product. An example of a report is a report that identifies the products that are most relevant to a business in terms of sales volume and resulting profitability.
- Price Analysis
The monitoring that this technology performs also allows you to analyze production costs. This is because the manager has the information needed to estimate the cost of raw materials, the time they remain in stock, the period required to produce the product, and wastage rates.
The system can have profit estimates for each product, which enhances the ability to make better decisions for business success. In this way, the need to change processes to provide greater flexibility and efficiency can be identified.
Best Inventory Management Practices
The need to manage inventory to save money has led to the emergence of many models and methods. The most famous include the following:
- Wilson’s model. It is considered the simplest because it does not involve the presence of uncertainties. The model allows you to determine the optimal level of reserves for the entire assortment, the criteria being the level of demand, placement costs and storage costs. It involves replenishing the warehouse at a certain frequency, in identical batches. The formula is suitable for companies producing products with stable demand, when the risk of unforeseen situations is practically absent.
- Just-in-Time model. It implies the delivery of raw materials and materials just in time, that is, exactly at the moment when they are needed on the production line, and in the quantity that is needed at the time of delivery. To reduce costs, the model practically eliminates the presence of a reserve in the warehouse, but when using it, the enterprise’s dependence on suppliers increases. Any supply disruptions can lead to shortages of raw materials and forced equipment downtime.
- ABC model. It consists of distributing reserves into three groups based on the method of volume-cost analysis. Category A includes stocks that are necessary for the most expensive products with a long use cycle. They account for the majority of the funds, so strict control is carried out on group A, and the required volume and costs are accurately determined. Group B includes raw materials and supplies for mid-price products. Category C is the cheapest inventory with high turnover and minimal markup.
What makes inventory management so difficult for most people is that there is no one right way to do it. The inventory management model that an enterprise uses must first of all take into account the specifics of a particular production. There is no single universal algorithm for everyone.
Ready-made Solutions in Advanced Order Export for WooCommerce
Fortunately, there are ready-made solutions available that can help companies master their inventory management. Advanced Order Export for WooCommerce is one such solution that can simplify the process and help businesses better manage their inventory.
With Advanced Order Export for WooCommerce, businesses can automatically export orders from their sales channels, such as ecommerce stores, marketplaces, and POS systems, to their inventory management system. This eliminates the need for manual data entry and reduces the risk of errors. It also allows businesses to have real-time visibility into their inventory levels, enabling them to make better decisions about stock levels.
We have prepared 3 ready-made solutions for you that will help you optimize your order management process:
Note: All reports have a checkbox Summary Report By Products. This is an important setting — it allows you to take overall statistics for the product.
Automatic scheduled summary by products CSV report, the destination of which is email.
First of all, we set up the Export Now tab. We leave the Filter orders by — Order Date. We leave the date range as default, so data for the entire time will be exported. If you want to export by specific order numbers, then specify a range of orders. The export file name can be customized by tags. Using them, for example, you can get the current date in the name of the report. You can view the tags using the link next to the file name or here. Let’s select the information with what status will be uploaded. Choose Completed.
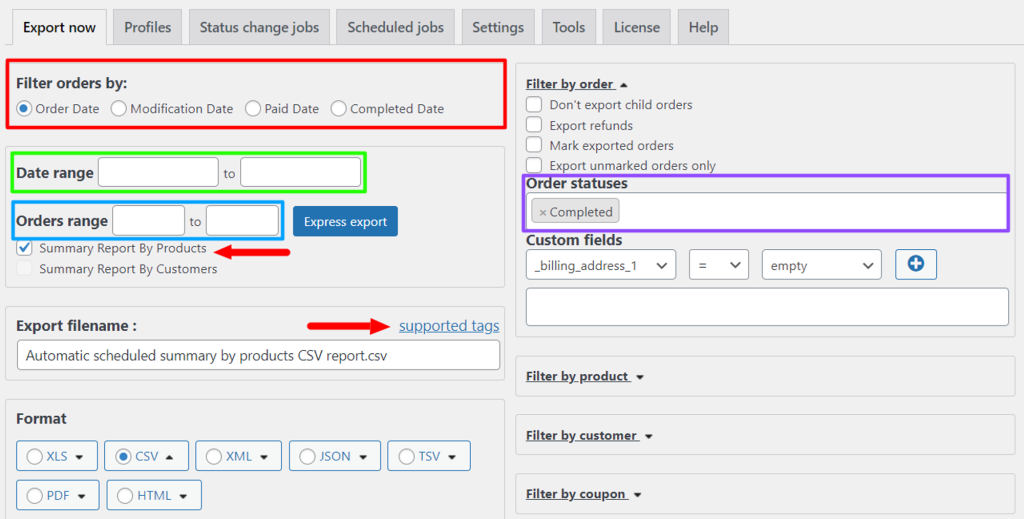
Let’s select the CSV file format. The settings can be left as default.
When you clicked the Summary Report By Products checkbox, the report automatically changed the fields to the appropriate ones:
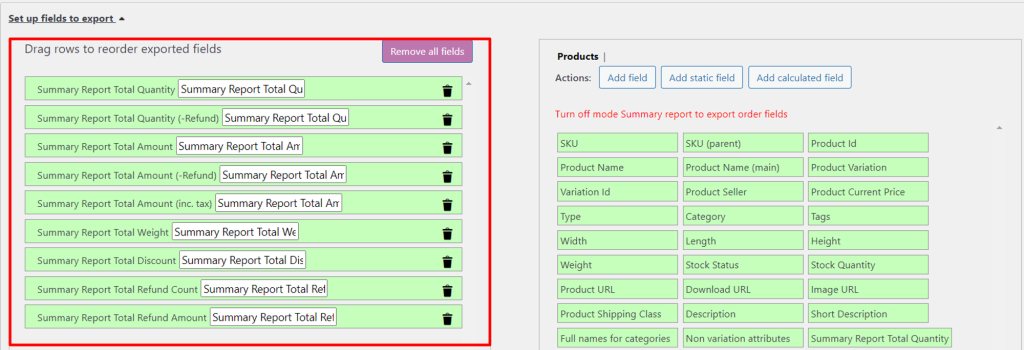
Let’s add other fields to them:
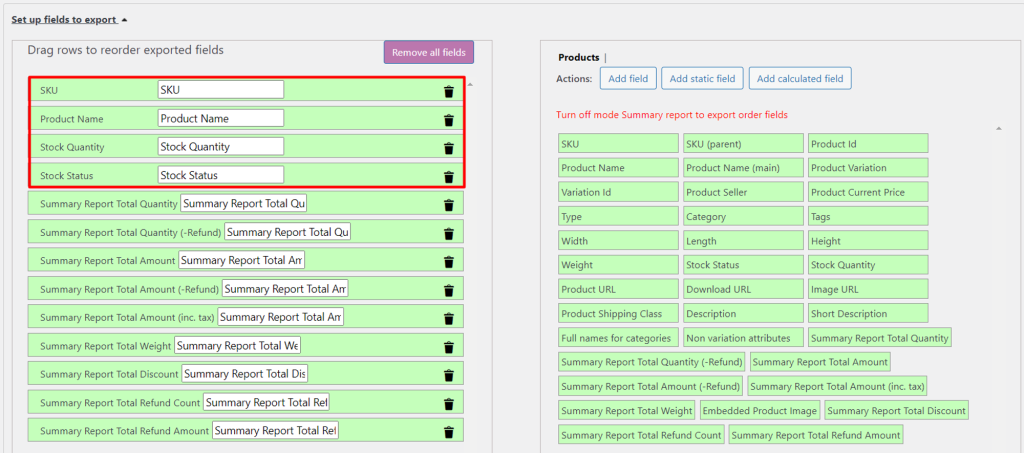
Save your settings and export this report:
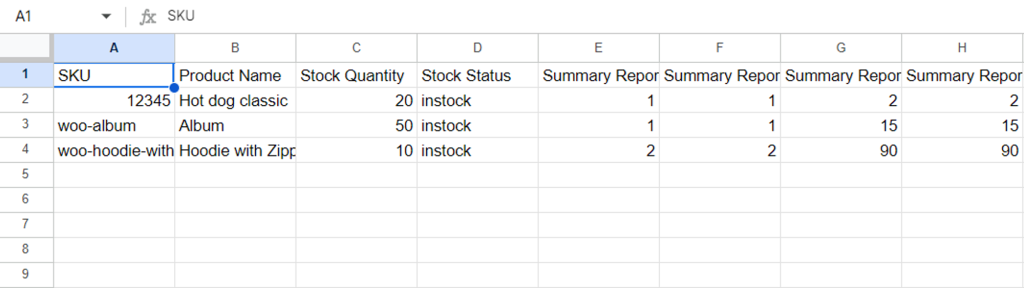
Click on the Save as profile button. Go to Profiles. Click on the clock button in the line with this report to add it to your scheduled ones.
Click OK in the pop-up window.
In the new tab, give your profile a name.
Select the exported date of the report. For example:
- Every week
- Only on Sundays
- Once a day
In our case, this is December 1 at 7 am.
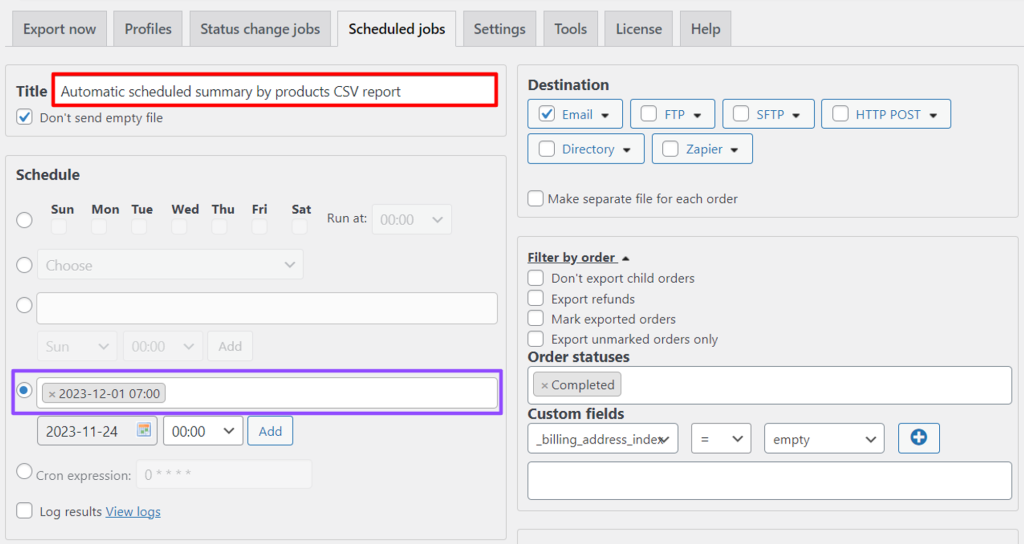
Let’s set up the directory. Select Email. Enter data in the following fields: From email, Email Subject, Recipients.
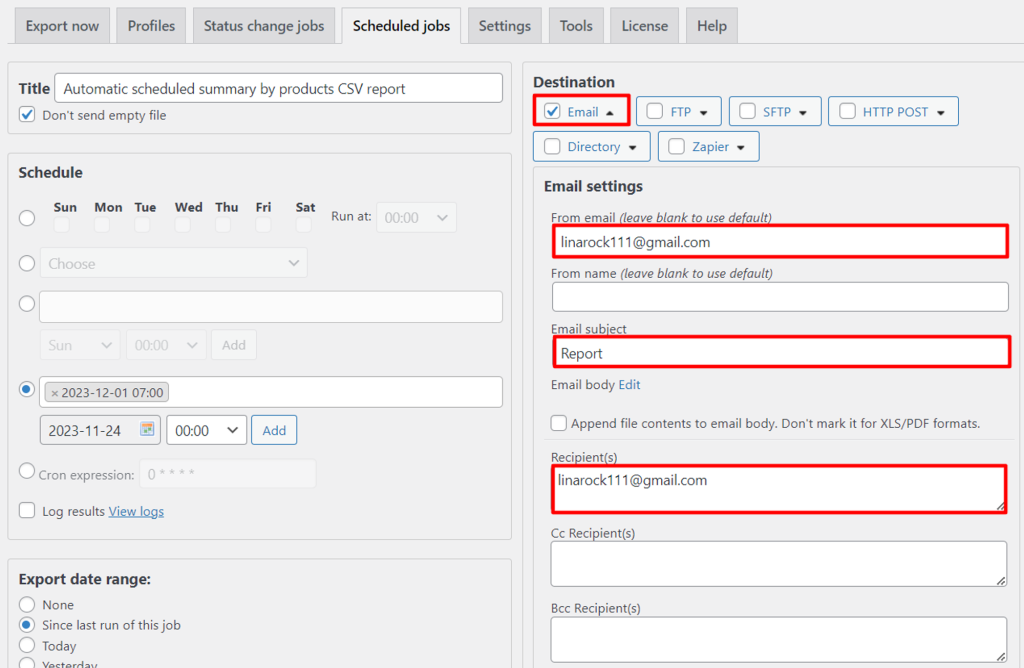
Click the Test button. If the submission is successful, you will see the following message:
File ‘Automatic scheduled summary by products CSV report.pdf’ has sent to ‘[email protected]’
Save your settings.
Automatic status change summary by products XLS report, the destination of which is Zapier (Google Docs).
We set up the second report in the same way as the first report. Select XLS format.
All the data is the same, so we won’t export the report.
When the Export Now is ready, save it as a profile. Let’s go to Profiles. Click on the button that looks like an arrow pointing to the right so that the report is uploaded when the status changes.
Click OK in the pop-up window.
In the new tab, give your profile a name.
Set the From status: Pending payment, Processing, On hold.
Status To: Completed.

Let’s set up a destination. Select Zapier.
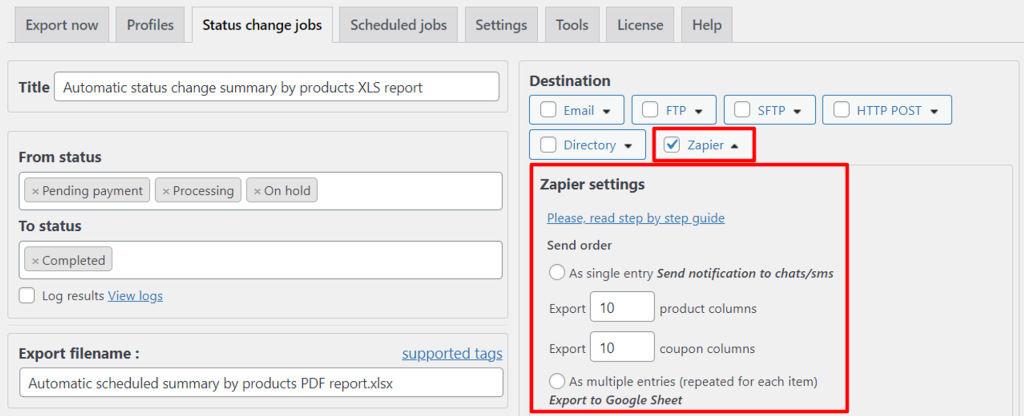
Note: feel free to read about how to connect job with Zapier here.
If Zapier is connected, then next to the job you will see the following text:
Connected to Zapier
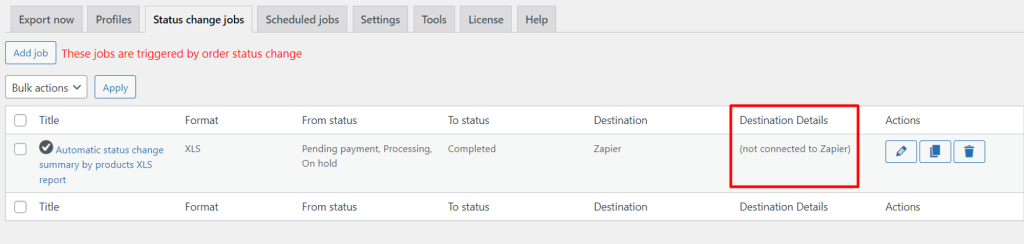
Save your settings.
Automatic scheduled summary by products HTML report, the destination of which is directory.
We set up the third report in the same way as the first report. Select HTML format.
All the data is the same, so we won’t export the report.
Click on the Save as profile button. Go to Profiles. Click on the clock button in the line with this report to add it to your scheduled ones.
Click OK in the pop-up window.
In the new tab, give your profile a name.
Select the date of the report. In our case, this is every Monday at 6 am.
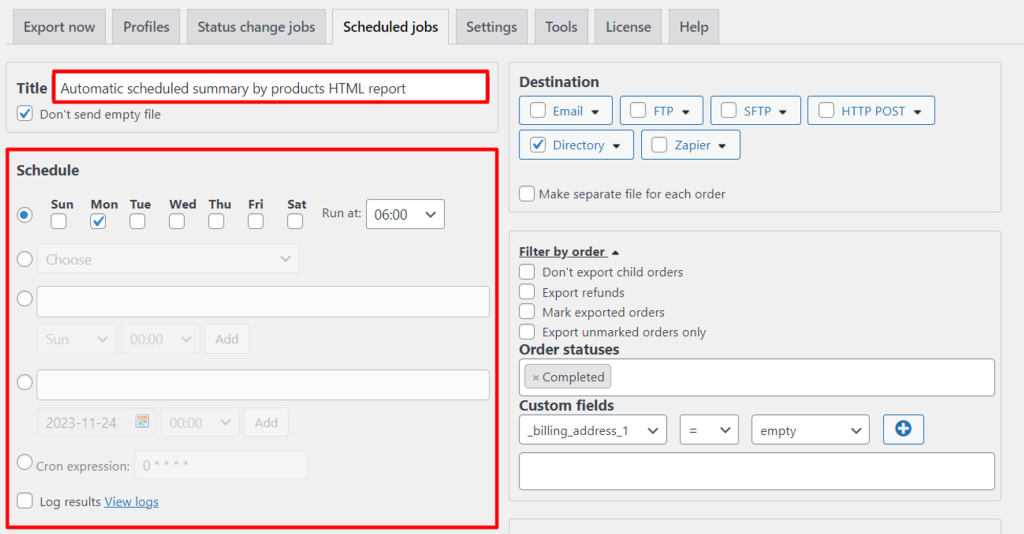
The destination this time is the directory. You can leave it as default and find the reports in the folder with your site.
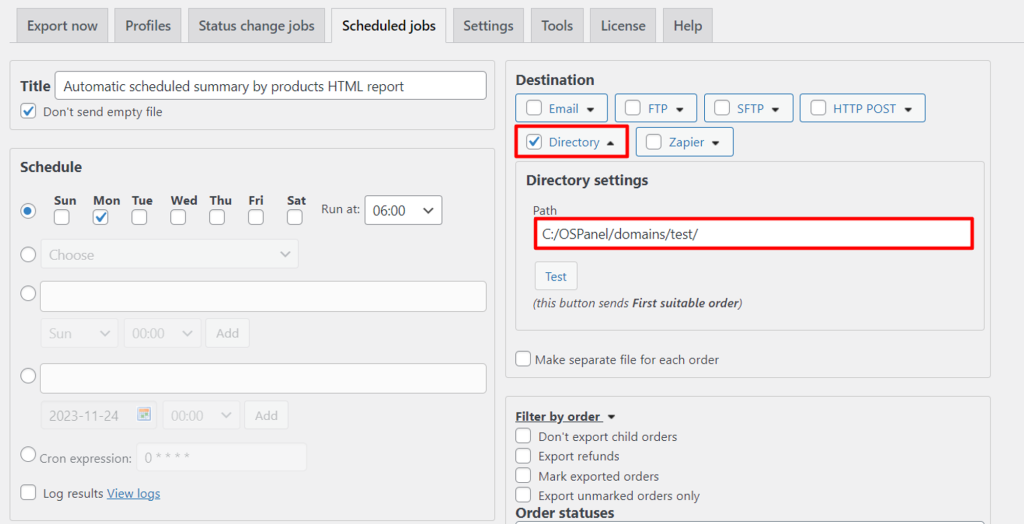
That’s it! Use Advanced Order Export for WooCommerce settings and save your time and effort.
Implementing inventory management isn’t just a good idea – it’s vital to business continuity and profitability, and proven trading technology provides a solution no matter the size of your business or the sector in which it operates.